The Science Behind Porosity: A Comprehensive Guide for Welders and Fabricators
Understanding the intricate devices behind porosity in welding is important for welders and producers striving for impeccable craftsmanship. From the make-up of the base materials to the intricacies of the welding process itself, a wide variety of variables conspire to either aggravate or ease the existence of porosity.
Recognizing Porosity in Welding
FIRST SENTENCE:
Examination of porosity in welding discloses crucial insights right into the stability and top quality of the weld joint. Porosity, characterized by the existence of dental caries or gaps within the weld steel, is an usual issue in welding procedures. These voids, if not properly addressed, can endanger the structural honesty and mechanical residential or commercial properties of the weld, leading to prospective failures in the finished product.
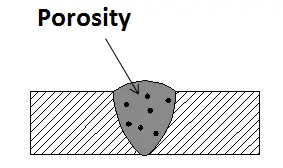
To find and quantify porosity, non-destructive testing approaches such as ultrasonic testing or X-ray inspection are usually used. These strategies permit the recognition of inner problems without endangering the stability of the weld. By evaluating the size, form, and distribution of porosity within a weld, welders can make enlightened decisions to enhance their welding procedures and accomplish sounder weld joints.
Variables Affecting Porosity Development
The occurrence of porosity in welding is affected by a myriad of factors, ranging from gas protecting effectiveness to the intricacies of welding criterion setups. Welding specifications, consisting of voltage, present, travel rate, and electrode kind, also effect porosity development. The welding method utilized, such as gas steel arc welding (GMAW) or shielded steel arc welding (SMAW), can influence porosity formation due to variations in heat distribution and gas coverage - What is Porosity.
Effects of Porosity on Weld Quality
Porosity development considerably compromises the architectural honesty and mechanical buildings of bonded joints. When porosity exists in a weld, it produces spaces or tooth cavities within the material, reducing the total strength of the joint. check over here These spaces function as anxiety concentration factors, making the weld more prone to fracturing and failing under tons. The visibility of porosity likewise deteriorates the weld's resistance to corrosion, as the caught air or gases within the gaps can react with the surrounding environment, resulting in destruction in time. Additionally, porosity can hinder the weld's capacity to endure stress or effect, additional threatening the general quality and reliability of the bonded structure. In critical applications such as aerospace, automobile, or architectural building and constructions, where security and toughness are paramount, the harmful results of porosity on weld quality can have extreme repercussions, highlighting the importance of reducing porosity via proper welding methods and treatments.
Methods to Minimize Porosity
Additionally, utilizing the suitable welding criteria, such as the right voltage, existing, and travel speed, is vital in preventing porosity. Maintaining a consistent arc size and angle throughout welding likewise helps reduce the chance of porosity.

Using the suitable welding method, such as back-stepping or employing a weaving motion, can also assist distribute heat uniformly and minimize the possibilities of porosity formation. By carrying out these methods, welders can properly lessen porosity and create top quality welded joints.
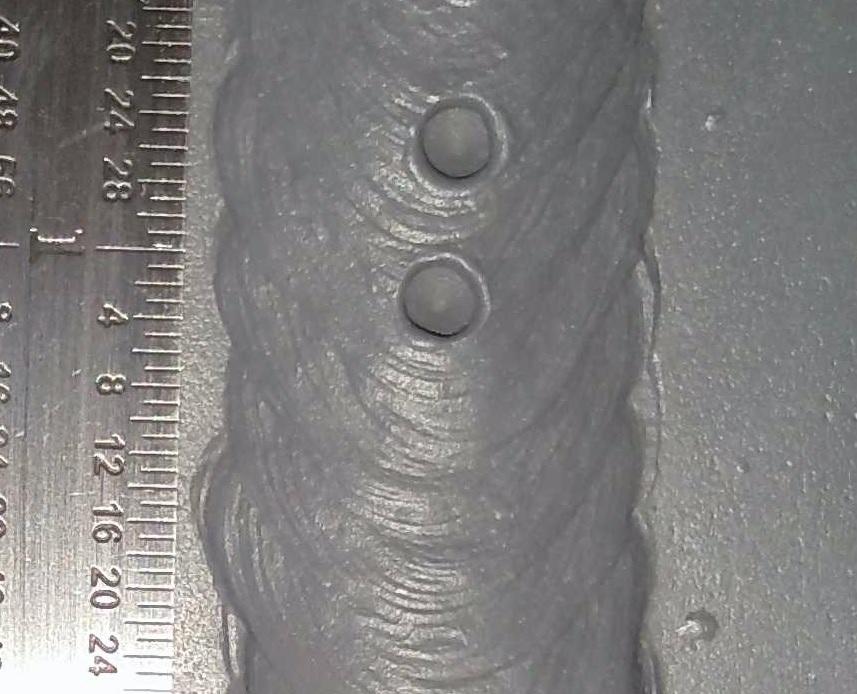
Advanced Solutions for Porosity Control
Executing innovative modern technologies view website and innovative approaches plays a pivotal role in attaining superior control over porosity in welding processes. One advanced service is making use of advanced gas mixtures. Securing gases like helium or a mixture of argon and hydrogen can these details help reduce porosity by offering much better arc stability and enhanced gas coverage. Furthermore, employing sophisticated welding strategies such as pulsed MIG welding or modified ambience welding can likewise assist alleviate porosity problems.
Another sophisticated solution entails using sophisticated welding tools. As an example, using tools with integrated features like waveform control and sophisticated power resources can enhance weld high quality and lower porosity risks. Additionally, the application of automated welding systems with specific control over criteria can considerably decrease porosity problems.
Additionally, integrating innovative surveillance and inspection technologies such as real-time X-ray imaging or automated ultrasonic screening can assist in discovering porosity early in the welding process, permitting instant rehabilitative actions. Overall, incorporating these innovative remedies can greatly improve porosity control and boost the overall high quality of bonded components.
Conclusion
In conclusion, understanding the science behind porosity in welding is crucial for welders and producers to produce top notch welds - What is Porosity. Advanced options for porosity control can even more improve the welding process and ensure a solid and reputable weld.